Load flow reactors also known as series reactors or line reactors, are critical components in electrical power systems. They are designed to regulate and control the flow of power within transmission and distribution networks. By adding inductive reactance to the system, load flow reactors help to manage power distribution, enhance system stability, and protect infrastructure from overloading. This detailed summary explores the function, benefits, design, applications, and maintenance of load flow reactors. Load flow reactors play a vital role in modern electrical power systems by regulating power flow, enhancing system stability, and protecting infrastructure from overloading and fault conditions. Their robust design, effective cooling mechanisms, and high-quality construction make them suitable for a wide range of applications in transmission networks, distribution systems, and industrial settings. Regular performance monitoring and maintenance are crucial to ensuring their long-term effectiveness and reliability, contributing to the overall efficiency and stability of the power system.

Reactors > Special Application Reactors
Load
Flow
Reactors
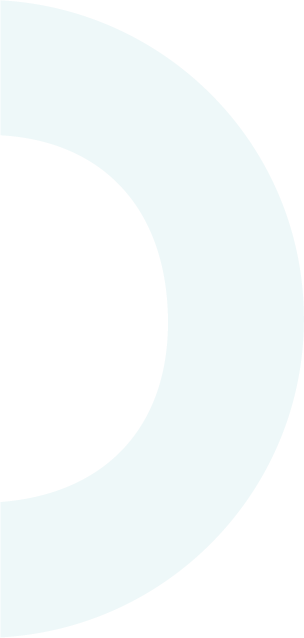
Function and Operation
1 Power Flow Regulation:
- Voltage Control: Load flow reactors are installed in series with transmission lines to regulate voltage levels. By introducing inductive reactance, they help maintain voltage stability across the network, preventing overvoltages and undervoltages.
- Current Limitation: These reactors limit the flow of current during normal and fault conditions. By controlling the current, they protect the system from excessive load that can damage equipment.
2 Impedance Adjustment:
- Reactive Power Management: Load flow reactors help in managing reactive power within the system. By adding inductive reactance, they counteract capacitive effects and improve the power factor.
- Load Balancing: They assist in balancing loads across different parts of the network, ensuring even distribution of power and reducing the risk of overloading any single component.
3 Fault Current Limitation:
- Short-Circuit Protection: During fault conditions, such as short circuits, load flow reactors limit the fault current, protecting transformers, switchgear, and other critical components from damage.
- Transient Suppression: They help in suppressing transients and surge currents that can occur due to sudden changes in load or switching operations.
Benefits of Load Flow Reactors
1 Enhanced System Stability:
- Voltage Stability: By regulating voltage levels, load flow reactors contribute to the overall stability of the power system. This stability is crucial for the reliable operation of sensitive equipment and the prevention of voltage collapse.
- Frequency Stability: They also help maintain frequency stability by managing the flow of reactive power, which can affect the system’s operating frequency.
2 Improved Power Quality:
- Harmonic Reduction: Load flow reactors can reduce harmonic distortion in the power system. Harmonics, often generated by non-linear loads, can interfere with the operation of equipment and cause heating in conductors.
- Reduced Flicker: By smoothing out fluctuations in power flow, they help to reduce flicker, which is particularly beneficial in applications requiring stable and consistent power supply.
3 Protection and Reliability:
- Equipment Protection: Load flow reactors protect transformers, circuit breakers, and other equipment from the stresses of high inrush currents and fault currents.
- Increased Reliability: The controlled power flow and enhanced stability provided by these reactors increase the overall reliability of the power system, reducing the likelihood of outages and equipment failures.
Design and Construction
1 Core and Coil Configuration:
- Inductive Reactance: The primary function of load flow reactors is to provide inductive reactance. They consist of coils of wire wound around a core, usually made from iron or other magnetic materials, to enhance inductance.
- Robust Construction: These reactors are designed to withstand high currents and thermal stresses. High-quality materials and precise construction techniques ensure durability and reliable performance.
2 Cooling Mechanisms:
- Air-Cooled Designs: Many load flow reactors are air-cooled, relying on natural or forced air circulation to dissipate heat. This design is simpler and more cost-effective for smaller reactors.
- Oil-Cooled Designs: Larger reactors often use oil cooling to manage higher thermal loads. The oil circulates through the reactor, absorbing heat and transferring it to external radiators or coolers.
3 Insulation and Protection:
- High-Temperature Insulation: Insulation materials used in load flow reactors are designed to withstand high temperatures and electrical stresses. This ensures long-term reliability and safety.
- Protective Enclosures: Reactors are often housed in protective enclosures to shield them from environmental factors, such as moisture, dust, and physical damage.
Applications
1 Transmission Networks:
- Voltage Regulation: In high-voltage transmission networks, load flow reactors are used to regulate voltage levels over long distances. This is essential for maintaining system stability and efficiency.
- Interconnection Points: They are often installed at interconnection points between different parts of the grid to manage power flow and ensure stable operation during varying load conditions.
2 Distribution Systems:
- Load Balancing: In distribution systems, load flow reactors help balance loads across different feeders, reducing the risk of overloading and improving power quality.
- Fault Management: They limit fault currents in distribution networks, protecting equipment and enhancing the safety and reliability of the system.
3 Industrial Applications:
- Motor Start-Up: In industrial settings, load flow reactors are used to manage the inrush current during the start-up of large motors, protecting the electrical infrastructure from damage.
- Power Quality Improvement: Industries with sensitive equipment or high-power demands use load flow reactors to improve power quality and ensure consistent operation.
Performance Monitoring and Maintenance
1 Regular Inspections:
- Visual Checks: Regular visual inspections are essential to identify signs of wear, damage, or overheating. This helps in early detection of potential issues.
- Thermal Imaging: Thermal imaging can be used to monitor the temperature of the reactor, identifying hotspots that may indicate excessive heating or insulation failure.
2 Electrical Testing:
- Impedance Measurement: Periodic measurement of the reactor’s impedance ensures it continues to provide the necessary inductive reactance. This helps in verifying its performance and identifying any deviations.
- Insulation Testing: Insulation resistance tests are conducted to ensure the integrity of the insulation materials, preventing breakdowns and ensuring safe operation.
3 Preventive Maintenance:
- Routine Maintenance: Implementing a preventive maintenance schedule helps address minor issues before they escalate. This includes cleaning, tightening connections, and replacing worn components.
- Proactive Repairs: Proactive repairs and component replacements ensure the long-term reliability of load flow reactors, reducing the risk of unexpected failures.