Traction duty inductors are specialized dry-type reactors designed with an iron core, tailored specifically for use in locomotives and railway traction systems. These inductors play a critical role in ensuring the safe and efficient operation of traction systems by managing current flow and mitigating harmonics. The primary design challenges for these inductors revolve around achieving compactness and reducing weight, which are essential for fitting within the limited space available in locomotives.

Reactors > Special Application Reactors
Traction duty Reactor
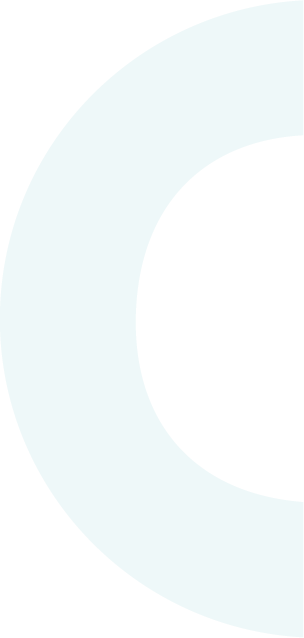
Design Considerations
1 Compactness and Weight Reduction:
- Space Constraints: Locomotives have limited space for additional components, necessitating a compact design for traction duty inductors.
- Weight Constraints: Reducing the weight of inductors is crucial to minimize the overall load on the locomotive, contributing to better fuel efficiency and performance.
2 Material and Insulation:
- Iron Core: The use of an iron core is central to the functionality of these inductors, helping to increase inductance and improve performance.
- High-Temperature Insulation: To cope with the increased losses and resultant higher temperatures due to the compact design, advanced insulation materials that can withstand high temperatures are used. This ensures the durability and reliability of the inductors under strenuous operating conditions.
Functions and Performance
1 Current Limiting:
- Initial Rate of Rise: Traction duty inductors are designed to limit the initial rate of rise of current during a DC fault near the traction substation. This is crucial in preventing damage to the electrical components and ensuring the safety of the traction system.
- Fault Management: By controlling the surge of current during faults, these inductors protect the substation and associated equipment from potential overloading and damage.
2 Harmonic Reduction:
- Harmonic Currents: In traction systems, non-linear loads can generate harmonic currents, which can interfere with the overhead wiring and overall system performance.
- Mitigation: Traction duty inductors help to reduce the flow of harmonic currents to the overhead wiring, thereby improving power quality and reducing electrical noise and potential interference with signaling and communication systems.
Operational Benefits
1 Enhanced Safety:
- Protection Against Faults: By limiting the rate of rise of fault currents, these inductors enhance the overall safety of the traction system, protecting both the infrastructure and personnel.
- Reliability: The use of high-temperature insulation materials ensures that the inductors can operate reliably even under extreme conditions, reducing the likelihood of failure.
2 Improved Efficiency:
- Reduced Harmonics: By mitigating harmonic currents, traction duty inductors contribute to the smoother operation of the traction system, reducing losses and improving energy efficiency.
- Optimal Performance: The compact and lightweight design of these inductors allows for optimal performance of the locomotives without adding unnecessary weight or taking up excessive space.
3 Longevity and Durability:
- Thermal Management: The advanced insulation used in these inductors ensures that they can handle higher temperatures without degradation, contributing to a longer lifespan and reduced maintenance requirements.
- Robust Construction: The iron core and durable materials used in construction make these inductors robust and capable of withstanding the harsh operational environment of railway systems.