
Transformers
Arc Furnace Transformers
Powering Heavy-Duty Metallurgical Processes
Arc Furnace Transformers are specialized transformers designed to supply the high current and low voltage necessary for the operation of electric arc furnaces (EAFs) used in steelmaking, foundries, and other metallurgical processes. These transformers are engineered to withstand the extreme electrical and thermal stresses associated with arc furnace operations, which involve frequent short circuits, heavy load fluctuations, and the generation of significant heat. Due to the demanding nature of their application, Arc Furnace Transformers are robustly built, with advanced cooling systems, durable insulation, and custom configurations to ensure reliable and efficient performance in harsh environments.
Key Functions and Benefits
1 High Current Supply
Electric arc furnaces require large currents to create and sustain the arc used for melting metals. Arc Furnace Transformers are specifically designed to provide the necessary high current, often in the range of tens of kiloamperes, while stepping down the incoming high voltage from the grid to a much lower voltage, typically between 100 and 1,000 volts. This high current supply is essential for maintaining the intense heat needed for the rapid melting and refining of metals.
2 Durability and Robustness
Arc furnace operations subject transformers to severe electrical and mechanical stresses, including frequent and intense short circuits caused by the arc striking process. Arc Furnace Transformers are constructed with heavy-duty materials and reinforced insulation to withstand these conditions. They are built to handle repeated on-off cycles and the mechanical vibrations that occur during furnace operation, ensuring long-term durability and minimizing the risk of breakdowns.
3 Advanced Cooling Systems
The significant heat generated during the operation of electric arc furnaces necessitates effective cooling of the transformer to prevent overheating and ensure continuous performance. Arc Furnace Transformers are equipped with advanced cooling systems, which may include forced air, forced oil, or water-cooling methods. These cooling systems are designed to manage the high thermal loads and maintain optimal operating temperatures, thereby prolonging the transformer’s lifespan and enhancing its reliability.
4 Flexible Tap Changers
Electric arc furnaces operate under varying load conditions, which require precise voltage regulation to maintain stable operation. Arc Furnace Transformers are often equipped with on-load or off-load tap changers that allow for the adjustment of the secondary voltage to match the furnace’s operational needs. This flexibility is crucial for optimizing the melting process, reducing energy consumption, and improving overall efficiency.
5 Harmonic Mitigation
The operation of electric arc furnaces generates significant harmonic currents, which can cause power quality issues in the electrical network. Arc Furnace Transformers are designed with features that help mitigate these harmonics, protecting both the transformer and the broader electrical system from potential damage and ensuring compliance with power quality standards.
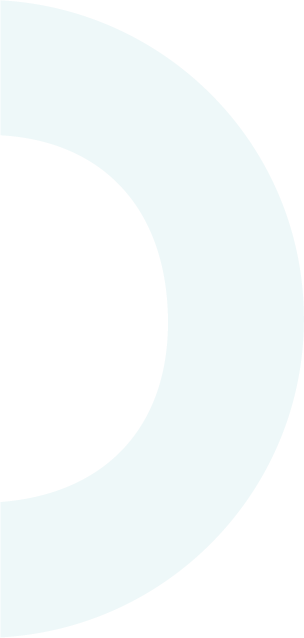
Applications
Arc Furnace Transformers are indispensable in industries that rely on electric arc furnaces, including:
- Steel Manufacturing Plants: Where they provide the necessary power for melting scrap metal and producing steel.
- Foundries: : For melting and refining metals such as iron, aluminum, and copper.
- Smelting Operations: In the production of ferroalloys and other specialized metals.
- Recycling Facilities: Where metal waste is melted down and repurposed.